The superior efficiency of electric deck systems makes them an increasingly attractive solution for bulk carrier operators amid rising costs and evolving regulations, says MacGregor.
As a world-leading provider of maritime cargo- and load-handling solutions, MacGregor offers an extensive portfolio of shipboard equipment for multiple vessel types. In the bulk carrier segment, its hydraulic cranes, hatch covers, and deck machinery – including anchor windlasses, mooring winches, and steering gears – are popular solutions with proven high standards in performance, safety, and reliability.
Yet with rising costs and evolving regulations emphasising the need for efficiency in every aspect of ship operations, there is a growing market for electric deck systems. In recent years, MacGregor has developed a comprehensive range of electric cranes, deck machinery, and hatch covers that provide an array of benefits to owners and operators of bulk carriers.
While cost has previously limited the uptake of electric deck solutions in the bulk carrier segment, owners are increasingly recognising the significant long-term savings they achieve by choosing an electric alternative over one using conventional hydraulics.
“Bulk carrier operators have been deterred from investing in electric systems due to the higher initial outlay,” says Carsten Sietas, Senior MacGregor Executive, Cranes. “That is now changing as owners come to realise the difference in cost between electric and hydraulic cranes isn’t all that great – while the savings enabled by electric solutions in the long run are considerable.”
Cranes
MacGregor’s electric cranes are highly efficient, Sietas explains, and can cut power consumption by up to 50%, resulting in significant savings in operating expenditure. The systems’ relatively low energy demands reduce fuel consumption by generators – and since alternative fuels are more expensive than oil, electric cranes will become even more valuable in the future.
When combined with other factors such as a streamlined installation process, the downsizing of auxiliary generators can partly offset the higher initial cost of electric cranes, minimising CapEx for both the ship owner and yard.
According to Sietas, the relatively simple configuration of electric systems can also help to cut OpEx, with one MacGregor case study showing a 22% reduction in service and spare-parts costs – amounting to a saving of up to $75,000 over 15 years. This is because many of the parts in a hydraulic system that require frequent exchange – such as hydraulic oil, hoses, and filters – are not present in the electric drive.
Another major benefit of the electric crane is its superior environmental performance. Helping bulk carriers to decarbonise by enhancing energy efficiency, the technology also eliminates the risk of oil spills, which pose a slip hazard and a threat to marine life. Reduced noise and vibrations also minimise environmental impact and enhance operator comfort.
Deck machinery
Similar benefits can be attained through electric deck machinery. With less need to include energy-reducing components than in hydraulic-electric systems, pure electric drives require a lower installed output and consume less fuel, achieving an efficiency rate of approximately 75–80%. For comparison, the efficiency rate of hydraulic-electric drives is typically around 50–60%.
“As with electric cranes, electric deck machinery enables significant OpEx savings – especially when factoring in its reduced maintenance and spare parts requirements,” says Thomas Kappel, Senior MacGregor Executive, Deck Machinery. “It is also more compact and easier to install than hydraulic-electric systems, while the absence of hydraulic oil makes it safer for the crew and the environment.”
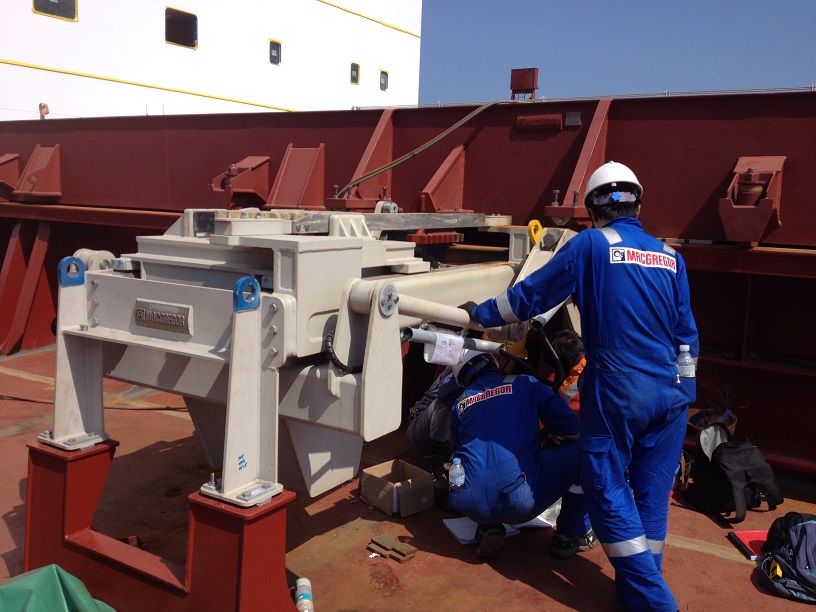
In addition, reliability, performance, and operational availability are maximised – and unplanned downtime minimised – through the combination of tried-and-tested components and cutting-edge technology, he adds. “The reduced operating cost of electric deck machinery, as well as its superior technical reliability and safety, make it a smart investment for bulk carrier operators.”
While some owners have expressed concerns about their crew’s ability to handle electric systems, Kappel explains that “we’ve observed the winch is relatively simple to operate, and it usually doesn’t require much time to train personnel in its usage”.
Hatch covers
The final component in MacGregor’s offering of electric deck solutions is its electric-driven hatch cover, which the company has been manufacturing and supplying since the early 2000s with E-Roll and, more recently, MacRack.
“Like our electric cranes and deck machinery, MacRack is more energy efficient than its hydraulic counterparts, enabling reduced OpEx and a smaller environmental footprint,” says Henrik Grönlund, Senior MacGregor Executive, Hatch Covers. “It also features a more streamlined design, with simpler, easy-to-maintain coamings; an absence of pipework and other hydraulic components; and a combined rack-and-pinion drive and lifter system that eliminates the need for separate hatch cover lifters.”
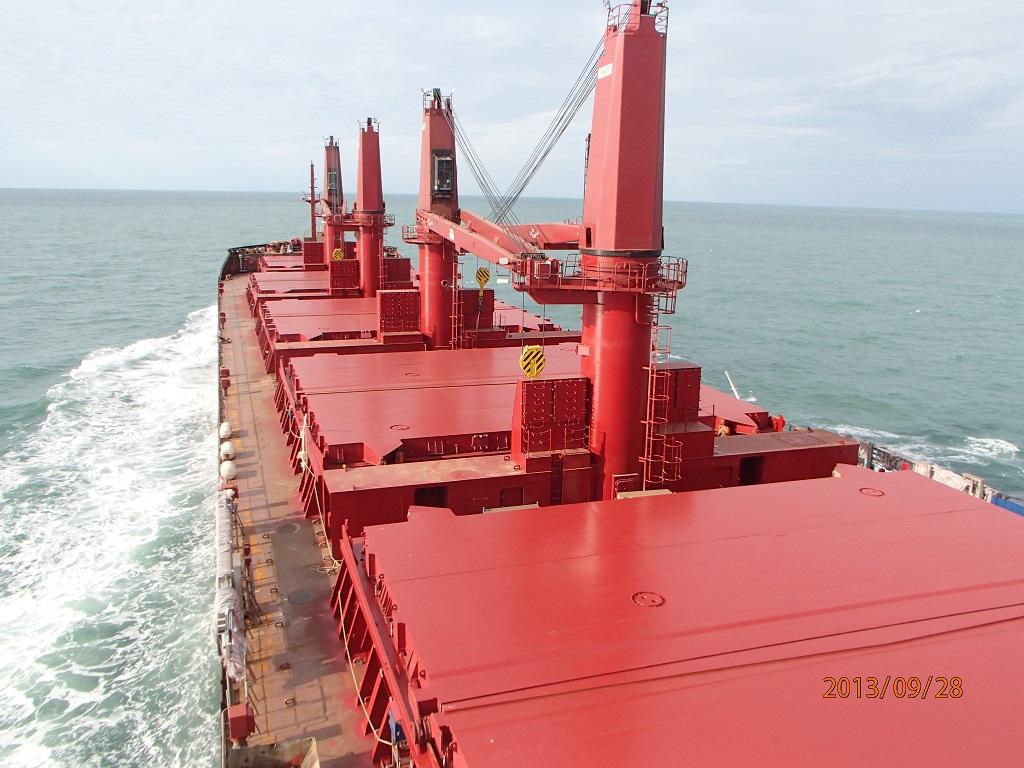
Furthermore, MacRack is easy to monitor and operate – an optional portable or wireless operating system is also available – and is more resistant to cold climates than hydraulic hatch cover systems, Grönlund adds.
A solution greater than the sum of its parts
However, the true value of MacGregor’s electric cranes, deck machinery, and hatch covers is realised when the three systems are deployed in combination, says Mattias Gunnarsson, Vice President, Newbuilding.
“With its superior efficiency, simplicity, and reliability, the cost-saving potential of the combined electric deck solution is huge, and the reduced power consumption enabled by all three components goes a long way to supporting regulatory compliance. Both factors are key to encouraging bulk carrier operators to adopt electric systems.”
Gunnarsson points to the complete elimination of hydraulic oil as an additional benefit of the combined electric deck solution and adds that the best time to install electric systems is during vessel construction.
“Installing all three electric deck solutions simultaneously is the most efficient approach, and by considering this at the ship design phase rather than for a retrofit project, owners minimise installation costs and downtime and maximise savings over the course of the vessel’s lifecycle.”
Meanwhile, the reliability and performance of MacGregor’s electric deck solutions can be further enhanced through connection to OnWatch Scout, which enables advanced monitoring and analytics for optimised systems availability and maintenance planning.
“For bulk carrier operators looking to reduce costs while enhancing environmental performance, reliability, and safety, MacGregor’s electric deck systems represent a simple, future-proof solution that comes with a multitude of benefits,” concludes Gunnarsson.
ENDS
Leave a Reply